Expert Weldment Techniques for Sheet Metal Fabrication
This post through the detail offered by the sheet metal fabrication parts manufacturer explains best practices, experience techniques employed in sheet metal fabrication, welding methods, and mistake avoidance.
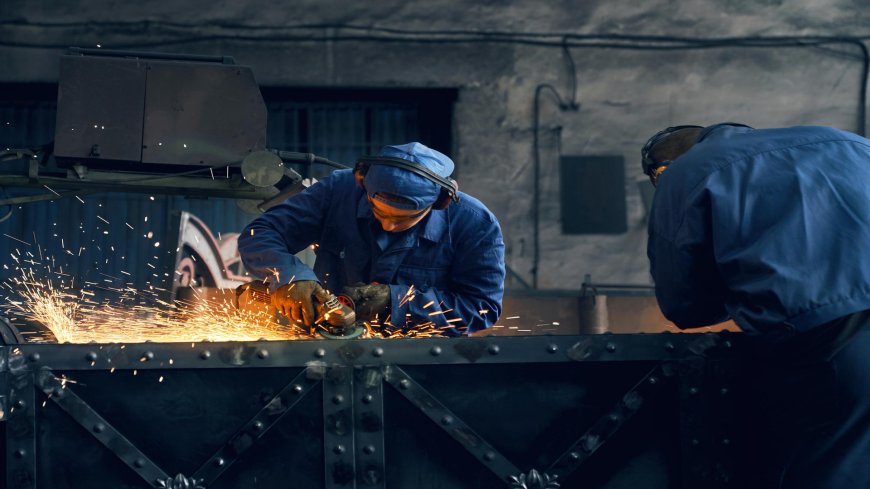
Sheet metal fabrication is the foundation of modern manufacturing, used in anything from auto panels to aircraft parts and consumer electronics. Weldment, the process of welding and forming discrete sections of metal into a single section, is perhaps the most important part of the operation. Well-controlled weldment must be done in order to transfer strength, functionality, and appearance to the end product.
This post through the detail offered by the Sheet Metal Fabrication Parts Manufacturer explains best practices, experience techniques employed in sheet metal fabrication, welding methods, and mistake avoidance.
Knowing Sheet Metal Fabrication Weldment
It is useful to define what a weldment is in sheet metal assembly before referring to individual techniques. A weldment is an assembly of metal components welded to each other in construction, usually stiffened by pieces like fasteners, brackets, or gussets. The assemblies range from as simple as a naked metal box to more complex, say, a motor vehicle chassis or air conditioner.
The aim of any weldment is to create a structurally sound, homogeneous piece to design specification, tolerance, and appearance requirements. Since the sheet metal is usually in the order of 0.5 mm to 6 mm thick and is ductile, accuracy when welding must be maintained so that warping, burn-through, and weakening of joints are avoided.
Choosing the Ideal Welding Process
Proper selection of the welding process is the key to the success of the weldment. The material type, thickness, application, and finish determine the welding process employed.
1. TIG Welding (Gas Tungsten Arc Welding - GTAW)
TIG welding is most commonly used in sheet metal work due to its precision and smooth surface finish. It is done using a non-consumable tungsten electrode and can be welded with or without filler material.
Best For:
- Stainless steel
- Aluminium
- Thin products
- Advantages:
- Low spatter
- Good welds, quality welds
- Good control
Considerations:
- Slower compared to most processes
- Requires high level of skill
2. MIG Welding (Gas Metal Arc Welding - GMAW)
MIG is faster and automatic and is used for high production volumes. It uses a coiled wire electrode and a shielding gas to create the weld.
Best For:
- Mild steel
- Aluminum (with quality wire and gas)
- Medium thickness
Advantages:
- Fast and efficient
- Easier to learn than TIG
- Less operator fatigue
- Variables
- More spatter than TIG
- Less control of heat, less control of weld size
3. Spot Welding (Resistance Welding)
Used to produce cars and appliances, spot welding uses flowing current to weld metal sheets in certain areas together to create welds.
Best For:
- Thin overlapped sheet metal joints
- Mass production
Strengths:
- Reproducible and fast
- No filler is needed
- Automated design
- Points to Ponder
- Restricted to overlapped joints
- Weaker with thicker materials
Master the Techniques of Quality Weldments
1. Material Preparation
Good preparation is the secret to a quality weld. Seasoned, veteran welders spend time to make sure:
- They are also oil-free, paint-free, or oxidized.
- Edges are deburred adequately to provide close joint fit-up.
- Fit-up tolerance is engineered to avoid gaps and misalignment.
- Poor preparation of material most frequently leads to lower quality joints, porosity, and contamination.
2. Heat Input Control
The characteristic of sheet metal is that it can be bent easily because metal sheets are thin in thickness. One of the main arts is controlling the heat input. Some of the key techniques are:
- Employment of pulsed welding processes in heat supply control
- Welding of small lengths (stitch welding)
- Providing cooling time for welds
- By the application of heat sinks or heat transfer backing bars
- The objective is to obtain adequate penetration without damaging surrounding metal.
3. Fixtures and Clamps
It is an issue to have components in the correct position, especially in those assemblies containing lots of components. Experienced jigs, clamps, and fixtures are used by skilled fabricators to keep components in the correct position. The gear:
- Limit distortion
- Improve accuracy
- Improve repeatability
- Robot welders can use accurate fixturing in automatic setups to create the same results.
4. Choosing Appropriate Filling Material
The filling material must be chemically and on melting point basis compatible with the base metal. Filler rods or filler wires are some examples of experts who:
- Duplicate base metal strength and resistance to corrosion
- Create aesthetic continuity (where welds must be left visible)
- Permit any follow-up operations like bending or painting
For example, in stainless steel welding, stainless filler rod is employed to enhance corrosion resistance.
5. Post-Weld Treatments
Welded parts typically involve finishing operations in the name of performance improvement and aesthetics. They cover:
- Finishing weld beads by grinding and sanding
- Passivation and pickling of stainless steel
Powder coat or protective corrosion paint Non-destructive examination (ND), such as dye penetrant or ultrasonic inspection of welds of vital significance An experienced fabricator considers how the weld will eventually be finished once the process is done and modifies his approach if needed.
Weldment Design Considerations
Elite weldment isn't simply a matter of technique—nor of design, for that matter. Fabrication and engineering coordination also ensure that weldments are easy to manufacture and sound good structurally. A few of the basic considerations in design are:
- Preventing joints from being too complicated and inaccessible or welds
- A reduction of distortion, for instance, by the use of balanced welds
- Choice of the proper kind of joint (lap, butt, T-joint, etc.) to apply
- Precise weld symbol identification of drawings in engineering drawings
- Computer-aided design packages and computer software simulation packages can also simulate distortion and heat transfer and aid more reasonable design decisions.
Conclusion
Sheet metal fabrication weldment skill is a case in point of the combination of technical knowledge, hand ability, and preparation.
From choosing the suitable welding method to manipulating heat in the attainment of close fit-up tolerances, the most successful fabricators understand that it is a case in point of the details. With increasingly complicated materials and production demands, the skill to accommodate new welding methods and design principles has to be acquired. From aerospace industry parts to everyday consumer household items, sheet metal fabricators, as welders, guarantee products not only to work but also to last. By mimicking master processes and accumulating experience step by step, you are then able to enhance the quality, lifespan, and productivity of every weldment that you make.
Also Read: Aluminum Car Parts: Exploring Its Process, Benefits, and Applications